CALS 3.0 produces a complete solution through the enrichment of design information, supply chain management and field logistics for the item’s lifecycle management. The new CALS 3.0 product family enables standardization and automation of operational processes. In addition to these, Carinafour offers several additional services as part of the CALS product family, such as Data and Analytics services.
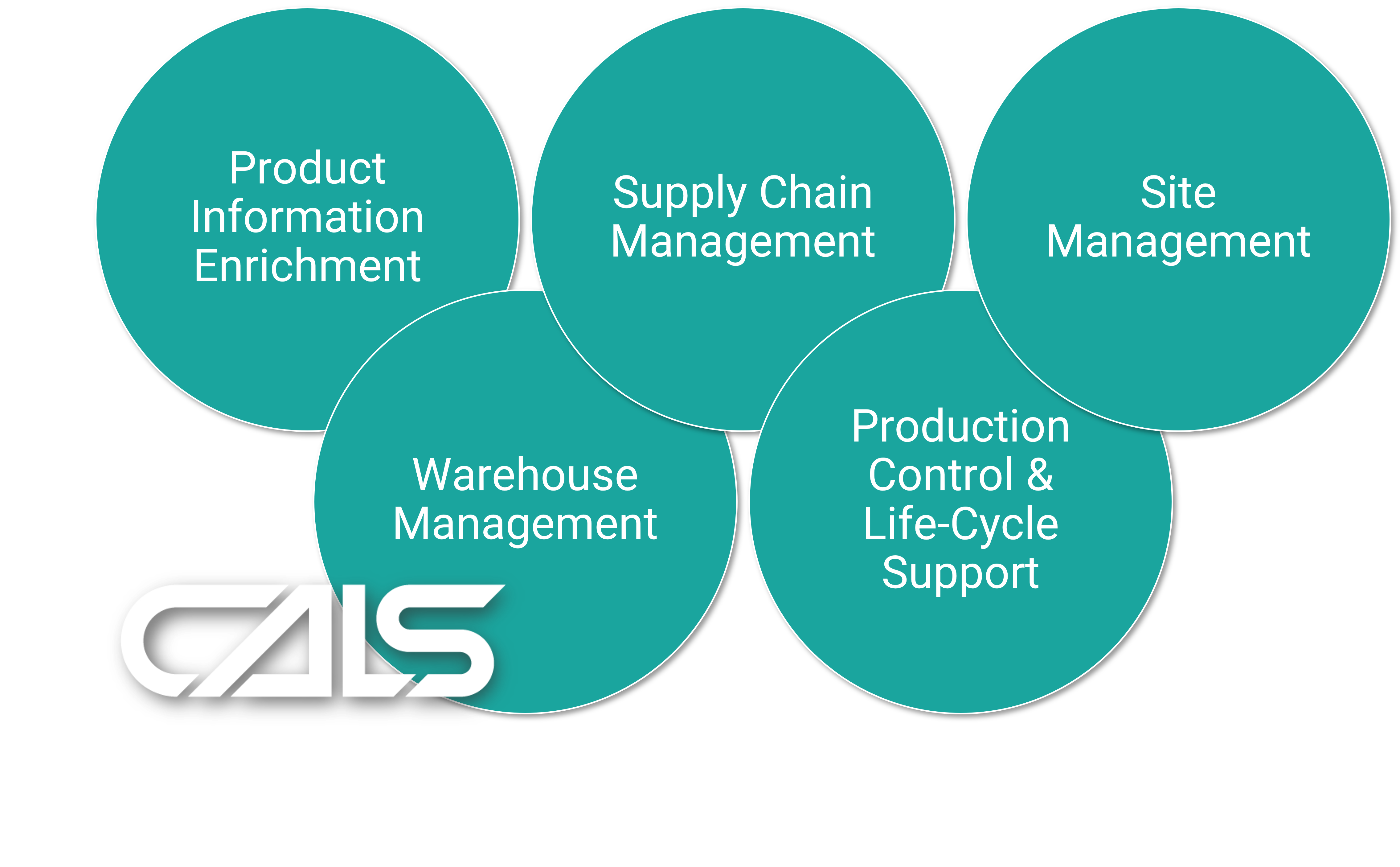
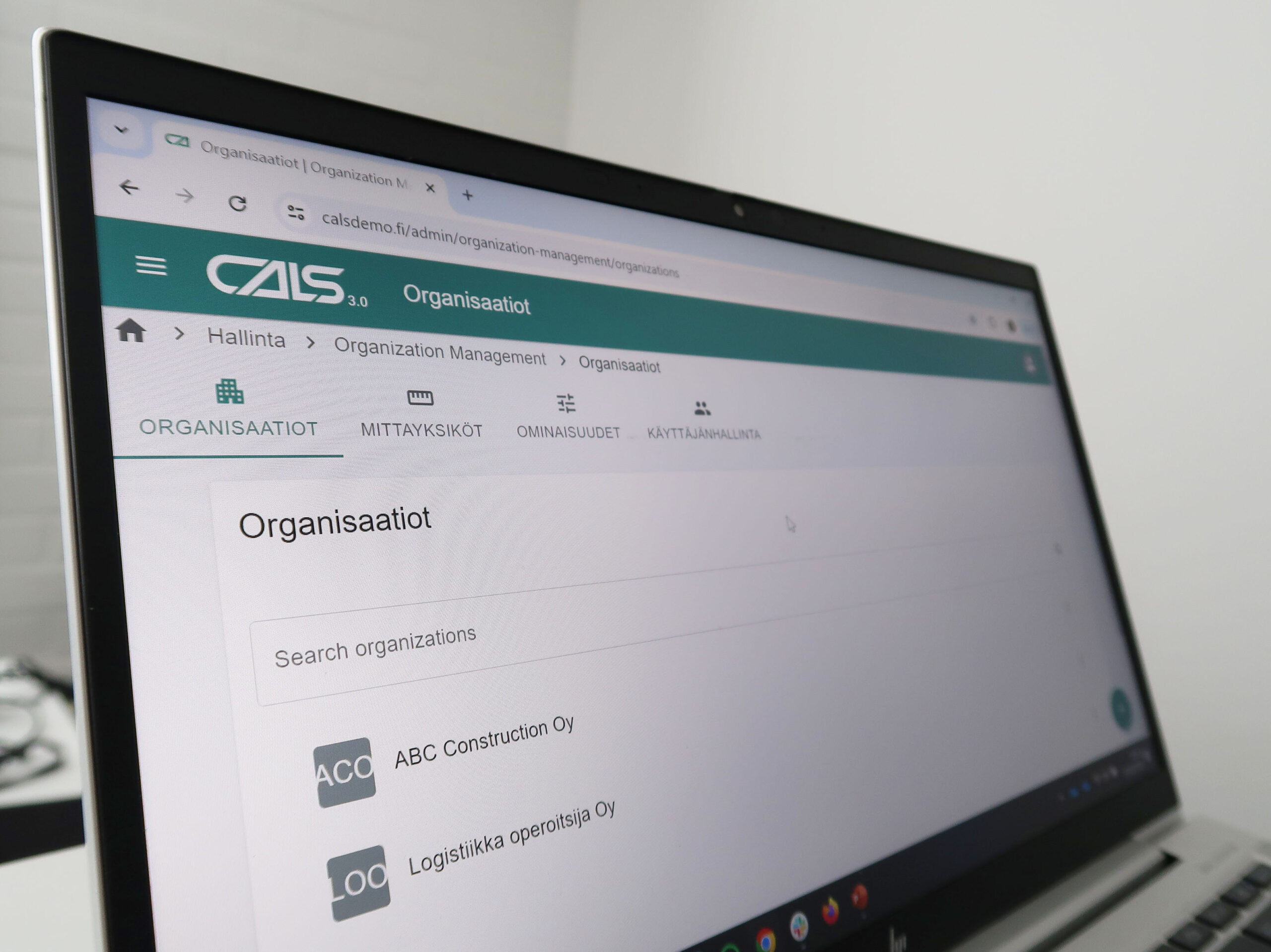
Product Information Enrichment – PIE – Standardization, learning and forecasting
- prepares space and work-phase -specific parts lists for supply chain
- enriches parts lists by adding, for example, missing item information or material details
- enables material selection management, for example, choices made by owner or resident
- enables creation of product dependencies and product sets
- uses company-based libraries in upcoming projects
- produces demand information for production planning, logistics and quotation requests
Supply Chain Management – SCM – Design, forecasting and ensuring
- plans, schedules and routes space- and work-phase-specific material deliveries to the destination
- produces demand information for the supply chain
- orders the materials and executes a digital availability check with the supplier
- monitors order confirmations and deliveries
- manages back orders
- digitizes delivery information
- ensures the right materials are received and automates reception process
- collects deviation information
- generates automatically information for invoicing
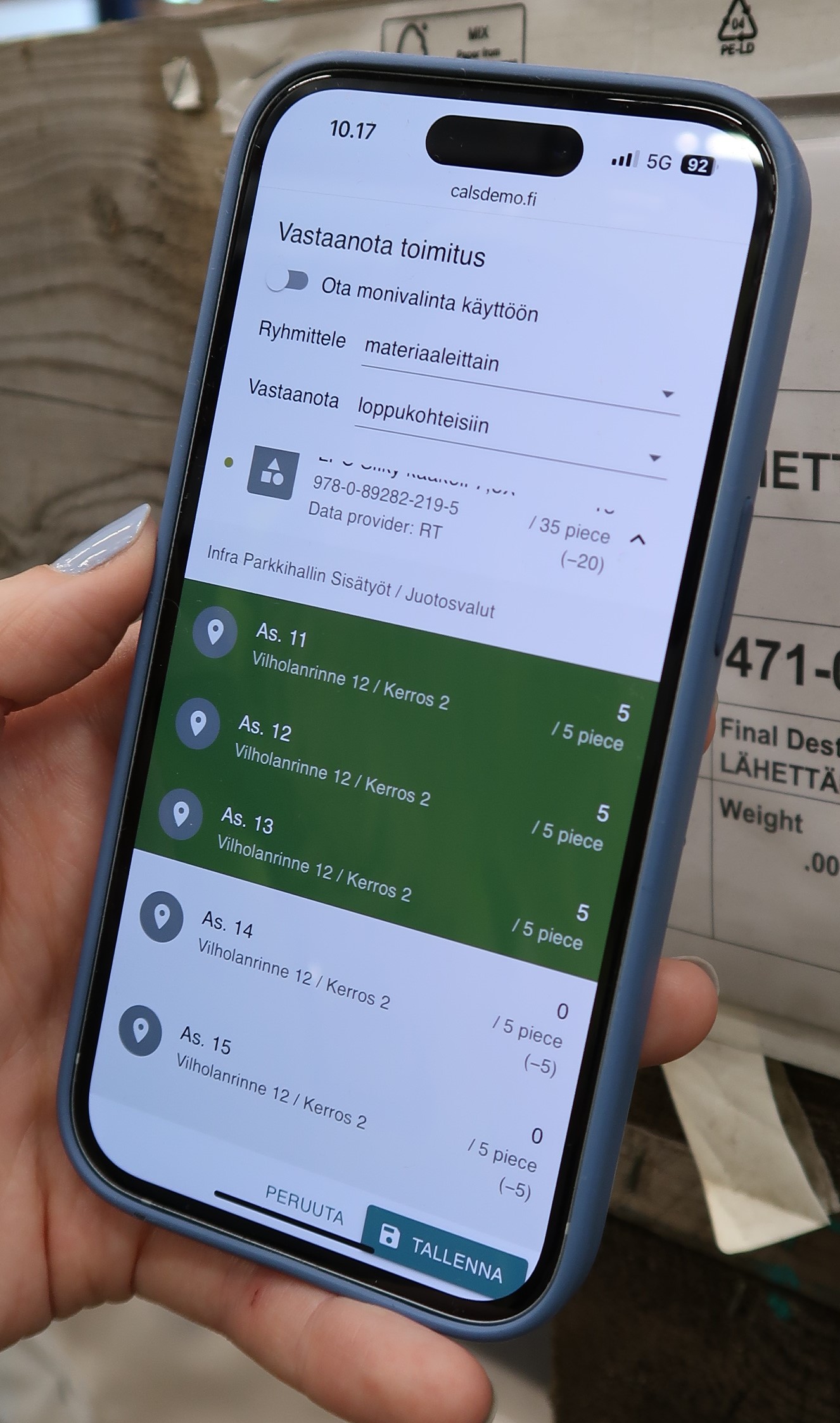
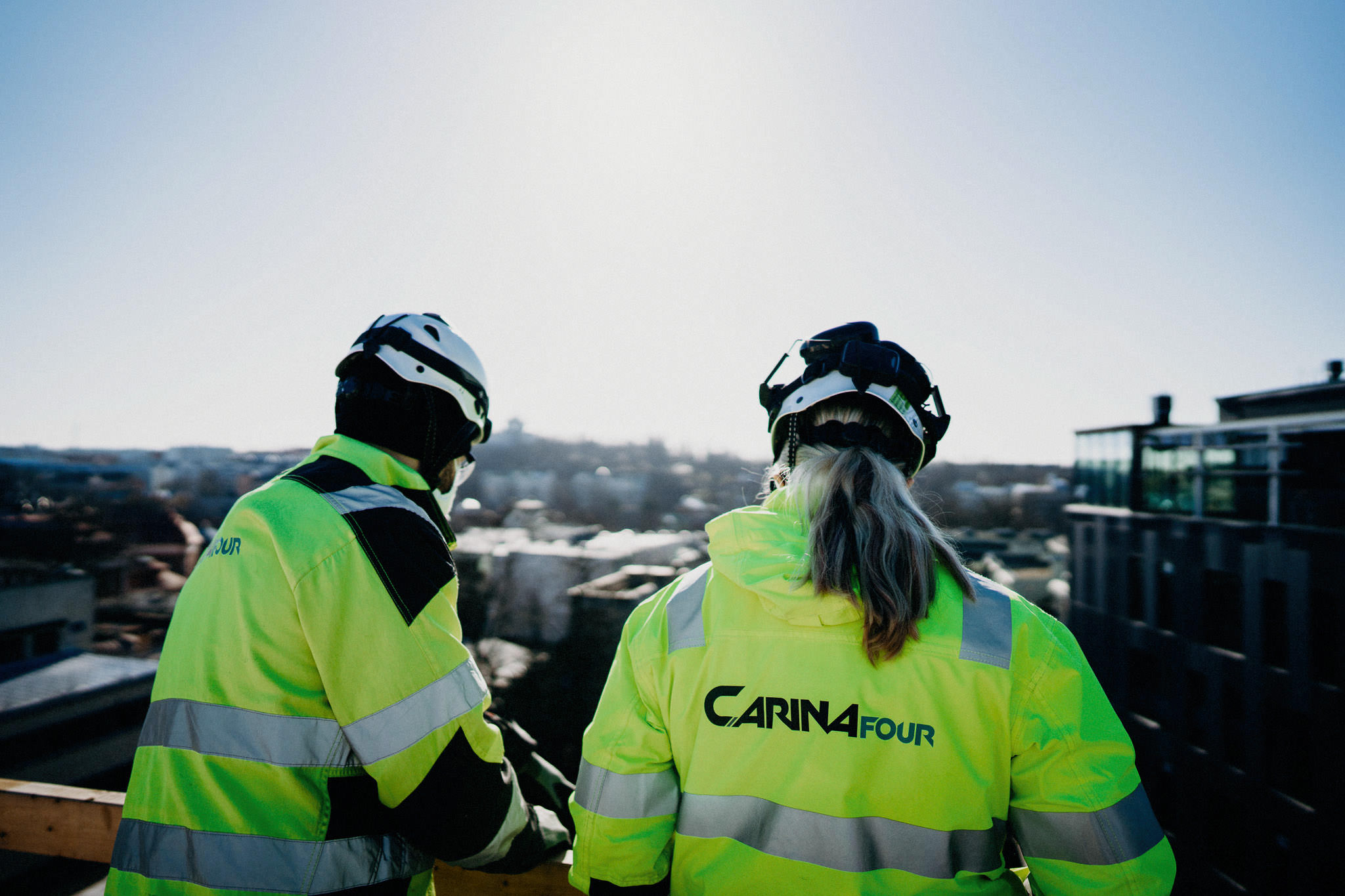
Site Management – Safe and efficient operations
- enables task budgeting, implementation monitoring, expense allocation and measuring logistics productivity
- plans unloading bookings, work tasks, allocation of resources and machinery, and different types of events in the same site calendar
- facilitates the reception and acceptance of completed work tasks
- designs safe hauling routes based on floor and yard plans
- ensures occupational safety in several ways
- collects information about occupational safety trainings and other qualifications needed at the construction site
- communicates task- and material-specific safety instructions
- enables digital approval of work and generates automatically information for invoicing
- collects customer feedback
- collects deviation information
- produces company-based task libraries for future projects based on completed projects
Production Control & Life-Cycle Support – Life cycle, realized product and product information
- ensures that materials are installed
- collects space-specific material information such as safety instructions and manuals in the handover material
- produces space-specific material information for lifecycle management
- enables calculations, for example CO2 calculations, based on the as-built information
- returns implementation data to the planned parts list and improves product management
- produces an evolving and more accurate product recipe for future projects
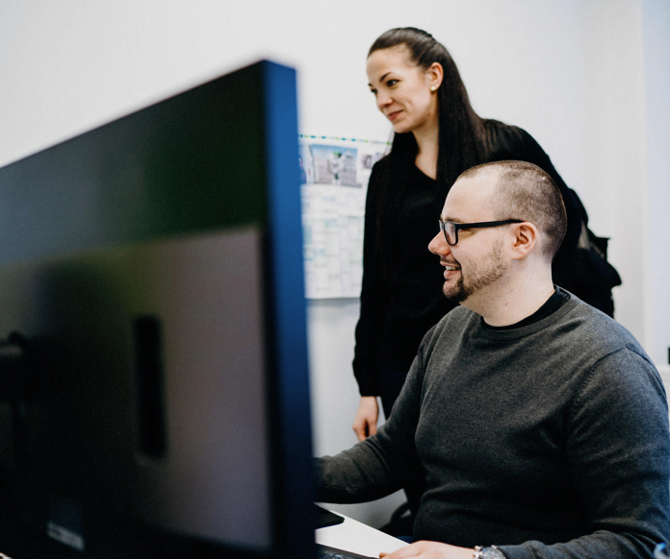
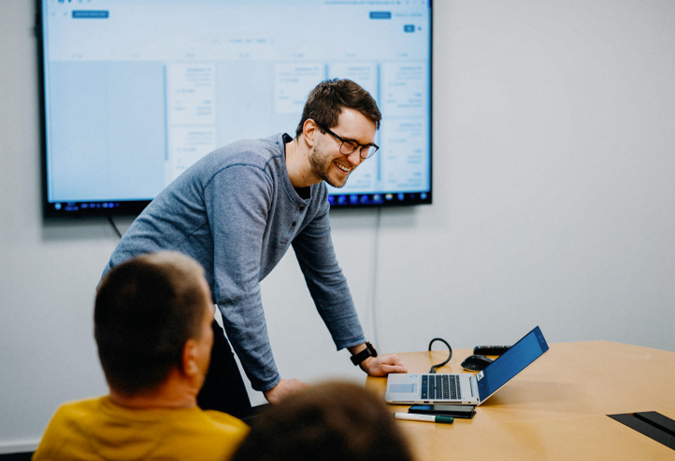
CALS Data & Management – Controlling and managing with data
- produces information for management and business development both at project and company level
- uses data to optimize operations
- provides basic metrics
- ensures operations are run based on the agreed process
- produces customized analysis service based on the customer needs